Tokusyu Kousyo Gijutsu “TKG” performs a variety of corresponding using ropes and special equipment, allowing repair and maintenance onshore and offshore at height.
Global Wind Organization Basic Safety Training Standards (GWO BST) Acquisition Status
To enhance our knowledge, skills, and confidence regarding the hazards connected to the wind industry, and to be able to respond appropriately to any emergency that might occur、while Having offshore operations in sight as our objective, 6 of our technicians have successfully acquired the GWO BST course including (first aid, manual handling, fire awareness, working at height, and sea survival).
In the following year 2023, a total of 18 technicians (7 from TKG and 11 from our partner company) are scheduled to attend the GWO BST course, bringing our total number of technicians to 24 ready to carry out offshore maintenance operations.
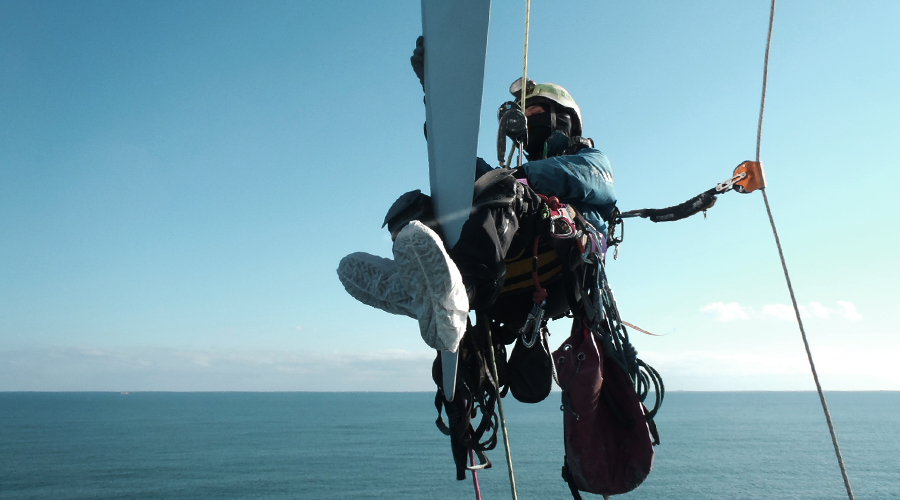
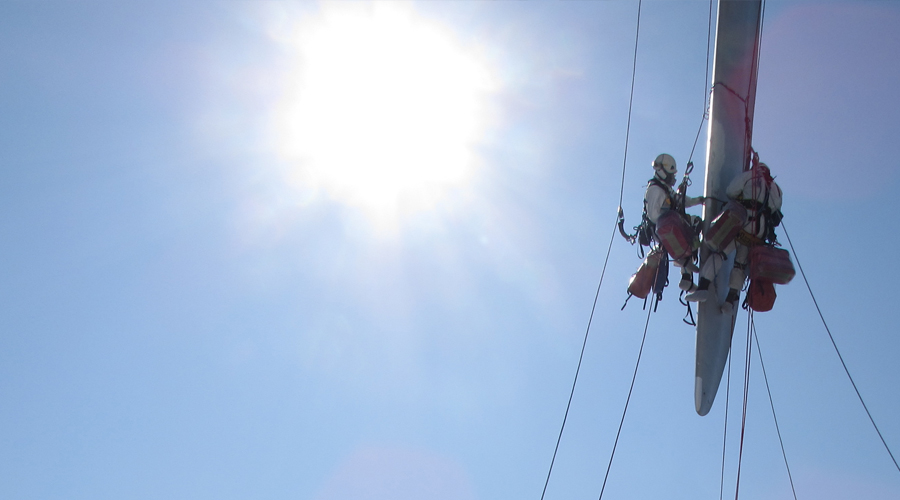
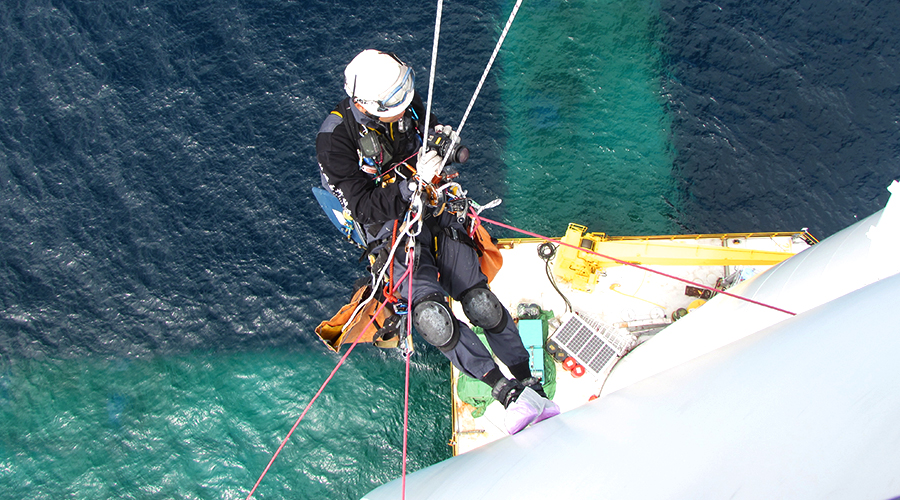
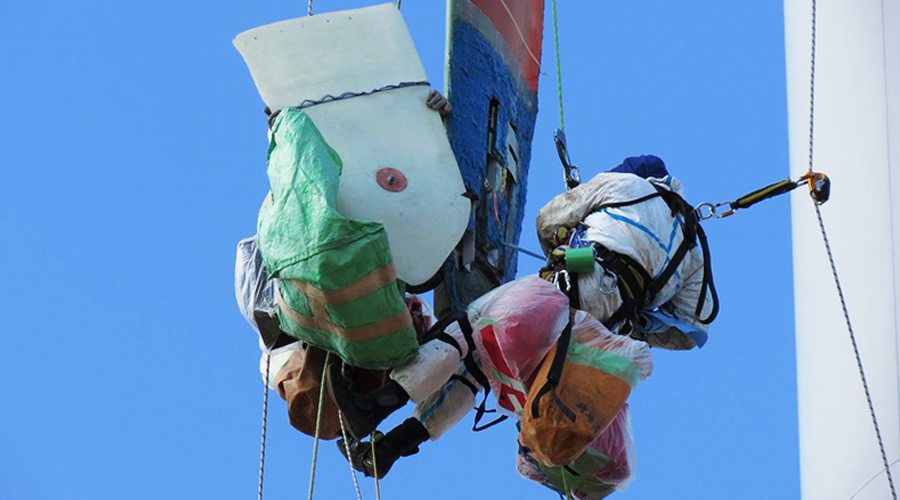
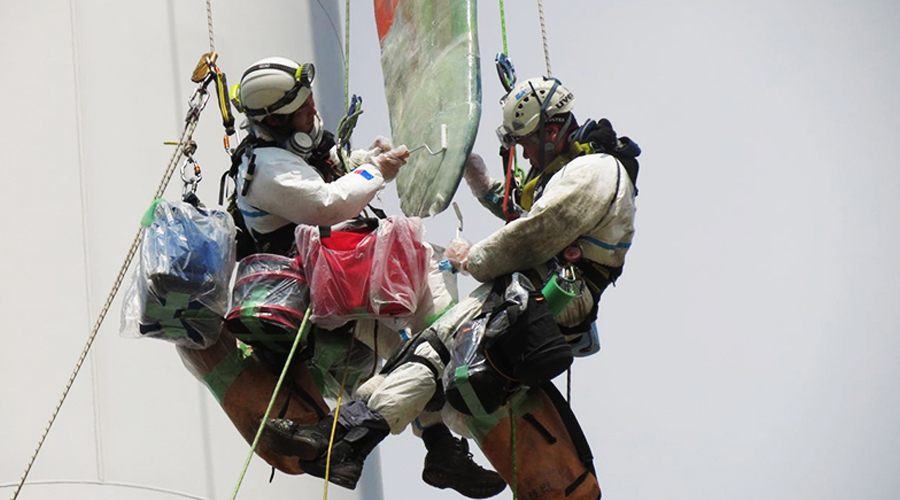

There is sound when playing video.Please be careful.
Periodic Safety Inspection “Regal requirement”
From April 2017, the regal requirement "Periodic inspection system" for wind turbines was enforced.
Basically, an "Inspection" is done every six months, one year, or three years depending on the part.
"Examination" for "Inspection" is every three years, but "Appropriate Operators" are given incentives and can be done every six years.
One of the requirements to be certified as an "Appropriate operator" is to have a "Continuous implementation system" carried by TKG will be the one way to be an "Appropriate operator".
Inspection and detailed investigation
TKG's engineers are not affected by the size and location of wind turbines, so we have a track record of maintenance offshore of 7 MW, the largest in Japan, as well as 5 MW and 3 MW.
The 7MW wind turbine has a blade length of 86m and a maximum width of more than 5m, but it is possible to approach from the root to the tip, enabling highly accurate inspection and detailed investigation.
Life cycle costs can be reduced by conducting inspections using TKG technology and repairing discovered damage at an early stage.
Blade repair work
Leveraging its experience with onshore wind turbines, TKG began repairing fixed-bottom offshore in 2011, and in 2014 it also began repairing floating type, we deliver the same quality results as onshore.
When the blade tip was damaged due to a lightning strike, we performed molding work onsite.
Even if parts supply is difficult due to reasons such as the manufacturer no longer being available, maintenance costs can be reduced by performing consistent work from production to restoration.
Since there is little advance preparation for work and few materials and equipment are brought in, it is possible to start work the day after a defect is confirmed, making it possible to minimize downtime.
Other maintenance
Removal of corrosion and painting of tower flanges, repair of nacelle, water leakage caulking, removal of oil and grease leaks inside and outside the top tower, replacement of aircraft obstacle lights and pitch and yaw bearing seals, addition of joint bolts and nuts various tasks such as tightening are possible.